Additive Fertigung von endlosfaserverstärkten Verbundwerkstoffen: Von der Faser-Matrix-Auswahl über die Druckkopfentwicklung bis zum Faserverbund
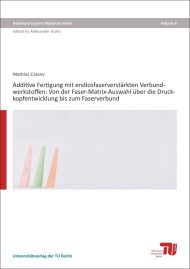
Format: 14,8 x 21,0 cm
Publishing year: 2022
The integration of endless fiber reinforced composites in additive manufacturing enables the automated production of materials with high mechanical properties such as strength. The current state of the art utilizing print heads with separate fiber and matrix feeds showed that, without active infiltration, the fiber infiltration is poor or not possible for thermoplastics with low flowability (high viscosity). In this work, the improvement of the print head technology and the investigated infiltration effect lead to a significantly higher infiltration. The material selection of thermoplastic matrix (PA6) and fiber reinforcement (carbon fiber) were adjusted for the new process parameters. The selection of the fiber matrix combination was conducted using the interfacial tension calculations at room temperature. The polar and dispersive surface energy of two different carbon fibers as well as the wetting of PA6 polymer melts on carbon fibers and on aluminum carriers were investigated. The calculation of composite properties using material data of the matrix and fiber was used to determine the process windows for specific parameters such as layer height, layer width and nozzle size. Furthermore, the mechanical properties and the cost of the composite can be determined in relationship with the materials used and the fiber volume content. The composition of the fiber sizing and the influence of high processing temperatures was characterized using TGA, FTIR spectroscopy and XPS analysis. The processing parameters and rheological behavior of PA6 thermoplastic resins and mixtures were investigated, and a mixture of 75 wt.% Ultramid B3k and wt.25% of Ultramid B50l from BASF was used for the composite fabrication by material extrusion. The optimization of the extrusion process enables the production of filaments with higher flowability (low zero viscosity), with the fiber infiltration improved by the adjusted rheological behavior. Samples for mechanical and optical analysis were fabricated using the self developed print head and three different types of carbon fibers. Three point bending properties were investigated as a function of layer height and printing temperature; tensile properties of single composite strands fabricated with different printing temperatures and multilayer composite were also characterized. The fiber volume content and the porosity were evaluated in crosssectional analyses. The investigated material combinations, optimization of process parameters and the fiber roving infiltration effect in the print head leads to higher mechanical properties and lower porosity in the composite.