Verfahrenstechnische Weiterentwicklung des Fused Layer Manufacturing zur Reduzierung der Anisotropie im Bauteil
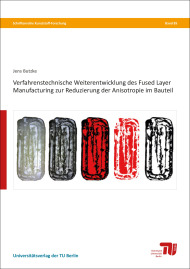
Format: 14,8 x 21,0 cm
Publishing year: 2019
Additive Manufacturing Processes are commonly used to generate prototypes in industrial environments. One such process is the 2½-dimensional Fused Layer Manufacturing (FLM) ptototyping process. The FLM uses thermoplastic filaments to create physical parts for initial investigations and inspections. However, the current FLM process is not capable of producing functional prototypes due to the weak interlayer cohesion of the parts. The weakness of the internal structure is due to the marginal interlaminar bonding of each layer to the top layer which is additionally overlapped by continiously generated notches inside the structure of the parts.
By using an enhanced low-cost FLM-device (at a cost of typically 1.000 €) with open build space and open-source software, it is possible to create a significant interlayer-bonding improvement. If the surface of the part is exposed to a higher temperature at the moment of joining, either by focused infrared radiation or the use of hot air, then the overall layer cohesion is significantly increased. The enhanced layer cohesion due to molecular entanglements can be quantified by impact-testing the parts according to the Charpy method, and the the optical appearance of the fracture surface is changed due to crazing. The improvement of the interlayer bonding is represented by the increase of impact energy. By optical microscopy it can be shown that layer cohesion is increased by use of the methodically developped process enhancements.
Identical test specimen were manufactured using a high-end FLM device (investment cost of the order of 15.000 €) with a build-chamber temperature of 75 °C, and were tested under similar conditions. The results here showed comparable interlayer-bonding as obtained by the low-cost FLM device, thus validating the improved deposition process developed for producing functional prototypes with a low-cost FLM device.