Untersuchungen zur Anwendung von Entfernungssensoren für Kleinsatelliten
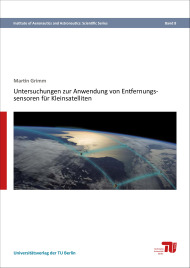
Format: 14,8 x 21,0 cm
Publishing year: 2019
Today the use of selected electrical, electronic and electromechanical commercial off-the-shelf (COTS) components in space applications is expanding. The main drive for using COTS in space is cost saving, but market non-availability, performance issues and a small form factor are further reasons to go for COTS. Small satellite missions in particular tend to apply COTS already more than others.
COTS parts usually do not meet the high reliability requirements for space applications. The lot-to-lot variations, the lack of traceability and the rapid obsolescence of such parts make qualification ineffective. Therefore, in this work a new approach to apply COTS for the use in space was developed and invesitigated on the example of distance measurement sensors.
Accurate distance information is important for satellite constellations and for rendezvous and docking maneuvers in space. Due to the advances in small satellite technology, missions involving multiple small satellites become more and more attractive. Maintaining an accurate distance in a close satellite formation can be crucial for system and safety issues. Furthermore, a cost effective distance measurement solution is particularly demanded for space debris removal, since the question of the financial responsibility is still unclear. Multiple cost effective distance measurement methods have already been proven reliable for distance measurements from far range down to about 30 m.
This work investigates various COTS distance sensors for measurements below 30 m for use on small satellites. With a combination of different COTS distance sensors with distinct measurement principles it is intended to prove that a fusion of the measurements of different sensors can help to counteract the degradation of the individual sensors under space environmental conditions. Furthermore, this could enable to maintain the accuracy of the overall distance measurement and to open up a possibility to lower system costs and to enable the use of state of the art technology in space applications.
For the investigation four different sensors have been chosen. The IVS-4005 was selected as a radar sensor. Two Mako G-125 cameras were combined to a stereo camera system. As a Photonic Mixing Device (PMD) sensor the EPC610 was selected. The close range distance measurements is additionally covered by the Time-of-Flight (TOF) sensor VL6180x.
Several environmental and stress tests were conducted to investigate the behaviour and the degradation effects for each sensor individually. For distances above 1 m the radar sensor provides the most accurate results. But the radar measurement principle alone is not able to reconstruct the targets alignment, rotation and shape. At even surfaces the success of a valid measurement furthermore depends on the viewing angle due to its measurement principle. The PMD EPC610 distance measurements show a high sensitivity against ionizing radiation. All four tested PMD sensors immediately suffered a drift of the distance measurement. As a solution for this degradation behaviour, a cross calibration approach was developed in this work. The cross calibration is based on applying the successful radar measurements which are stable under all environmental influences investigated to calibrate the PMD EPC610 sensor. So PMD EPC610 measurements shall be corrected by radar IVS-4005 distance values during a close range maneuver. The stereo camera system was rejected for the sensor fusion concept due to its disadvantageous measurement behaviour under space conditions.
This developed cross calibration approach was applied in a simulation including all observed degradation effects. The sensor fusion approach improves the overall measurement in terms of accuracy and successful detection sample rate compared to a single-sensor solution. At 25 m, the chance of correcting the high initial PMD sensor EPC610 offset with the radar sensor IVS-4005 is about 70 % with an uncertainty of 2 %. By this simulation, a weakness of the sensor system was identified from a distance of 3 m down to 0,2 m, which however can be counteracted by a replacement of the VL6180x sensor with its successor.