Variotherme Verarbeitung von Epoxidharz zur Zyklusverkürzung im RTM Prozess
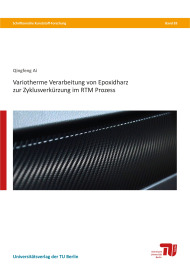
Format: 14,8 x 21,0 cm
Publishing year: 2018
In the present thesis a dynamic and variothermal RTM process has been established that, under application-oriented conditions, accomplishes the manipulation and regulation of the crosslinking reaction in an epoxy resin system. This development is motivated by the need to shorten production cycles in industry whilst ensuring at the same time the quality and conformity of the manufactured moulded parts.
In order to analyse the practical moulding process a systematic characterisation of the crosslinking reaction of the underlying material system is carried out in the first instance. For this purpose, based on a set of DSC measurements, a reaction kinetic model for the description of the curing process is derived that incorporates both, chemical and diffusion controlled parts of the reaction. By means of this model, conversion rates and glass transition temperatures can be described and predicted for arbitrary curing temperatures and times which in a further step allow, according to application and requirements, the appropriate tuning of process parameters in a practical manufacturing operation.
For validation purposes and in order to constrain the practical relevance of the derived reaction model, simple epoxy resin parts have been manufactured at a laboratory scale by a variothermal mould. The analysed curing states of the resulting parts perfectly fit into the model, thus providing verification. Via variothermal moulding at distinctly high curing temperatures the curing time to reach a defined degree of crosslinking could be significantly reduced, up to 90 %, in comparison to an isothermal reference process. However correlations among the cross-section of the mould, the degree of crosslinking, and the resulting part properties should be taken into account.
Furthermore the applicability of this procedure for industrial production of carbon fiber reinforced epoxy resin moldings (CFRP) was tested by using a variothermal RTM tool. An essential challenge was posed by the reasonable adjustment and realization of a dynamic and homogenous temperature control of the tool with a relatively large freeform surface. In order to implement a close-to-contour and contour-following fluidic temperature control, the present investigation combines conventional milling operations with thermal spraying process, thus leading to a stable and operationally reliable mould insert. Even by use of one-sided variothermal heating the conducted experiments reveal a shortening of curing time up to 50 % in comparison to the conventional process.