Über die Wirkung thermoplastischer Elastomere als Additive zur Unterdrückung des sharkskin-Effekts
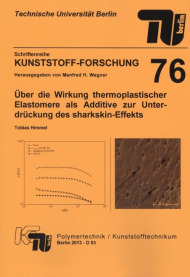
Format: 14,8 x 21,0 cm
Publishing year: 2013
The extrusion rate of polyethylene is limited by melt fracture. The first level of fracture is a surface defect called sharkskin. Common polymer processing aids based on fluoropolymers shift the onset of sharkskin to higher extrusion rates. These materials are expensive and carry some environmental concerns. Alternatively Kulikov (2005) suggested thermoplastic elastomers (TPE) for sharkskin suppression. Müller (2009) showed the usability for some TPEs as polymer processing aids. Both authors gave an experimental classification according to the efficiency of different TPE types for sharkskin suppression. The aim of the present work is to find the reason for the different efficiencies of TPEs for sharkskin suppression. The slip velocity of some TPE types against steel and the slip velocity in a polymeric interface between polyethylene (PE) and TPE were evaluated rheologically. Thereby, low viscosity types of TPE show a higher slip velocity against steel. The determined slip velocities were viscosity independent and of the same order of magnitude in the polymeric interface. In both cases the slip velocity is directly proportional to the applied shear stress. For further material characterization, measurements of first normal stress difference were done. The data correpond well with the empirical rules proposed by Laun (1978, 1986). Neither differences in silp velocities nor in normal stresses explain the different efficiency of TPEs for sharkskin suppression. It is the interfacial tension between PE and TPE that shows to be the reason for the different efficiency in sharkskin suppression. As described by Pötschke et al. (1997, 2002), the chemical structure of the soft segments in TPEs lead to different grades of dispersion of TPE droplets in a PE matrix. TPEs based on polyester or silicone have a coarse structure with big droplets. This is due to the two phase character of the TPEs, where hard and soft segments are located next to each other. Consequently, a phase segregation occurs in the TPE in the polymer melt. The soft segments aggregate in contact to PE driven by surface tension at the interface and influence their properties. In agreement with the work of Oriani and Chapman (2003), the efficiency of polymer processing aids for sharkskin suppression increases with droplet size. Thus, the efficiency of TPEs as polymer processing aids for sharkskin suppression follows from the phase segregation inside the TPE. The interfacial tension varies according to the chemical structure of the soft segments of the TPE. It is shown that the different interfacial tensions give different dispersion morphologies, leading to the conclusion that a coarse dispersion structure results in a better efficiency of the TPE for sharkskin suppression.