Nicht-intendierte Outputs bei der Gewinnung und Verstromung von Braunkohle
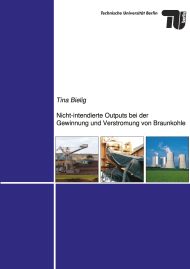
Format: 21,0 x 29,7 cm
Publishing year: 2010
For the activities of the lignite mining and the power generation from lignite land is occupied and equipment and energy are used. During operation various material and energy flows such as overburden, mine water, dust, exhaust air, ash, gypsum, energy, cooling water, waste water, coolant and lubricant losses etc. are released. The released material and energy flows are nearly always without value in the raw material supply chain and in the electric power supply chain. They are not the production targets of the mining industry and the power generation industry. Instead, they usually have negative effects on the economy and ecology and are, therefore, referred to as non-intended. The knowledge of the quantities and qualities of these non-intended outputs as a function of the individual processes and their parameters is the basis for technical and economical measures to affect them. In this thesis a methodology for the acquisition and assessment of the material and energy flows in the lignite mining and the power generation from lignite is presented. The methodology is based on an integrated approach due to the comprehensive technical and economic analysis of material and energy flow systems. A hierarchical system structure allows the precise assignment of the material and energy flows to the individual processes. Mathematical process models were deduced to characterise the chemical change of materials and the conversion of energy during processes. For modelling the overall system as a material and energy flow network and for calculating unknown material and energy flows in dependence on defined model parameters the software Umberto is used. The system analysis and the investigation of the general conditions for the lignite mining and the power generation in lignite-fired power plants in Germany show a complex overall system with many influencing factors. Using the example of mining in an opencast mine with conveyor bridge technology and mine water treatment together with the example of power generation in a conventional steam plant with the option of post combustion carbon dioxide capture and compression all the relevant non-intended outputs are determined and aggregated to characteristical indicators. The results of two case studies show that the quantity of equal lignite mined, conveyed and converted to electricity had to be nearly 1.8 times larger to produce the same amount of electrical power considering post combustion carbon dioxide capture and compression than without considering post combustion carbon dioxide capture and compression in the overall system. Thus the non-intended output flows significantly increase. If the necessary data is available for several systems the calculated indicators can be used for the purpose of a benchmarking to compare individual processes of the lignite industry or complete systems from mining to power generation to each other. Then appropriate measures can be derived for the choice of techniques and for operational practice, e.g. to reduce the costs, control emissions or save resources. Furthermore, it is possible to find criteria related to a specific site in order to optimise the operating and follow-up costs of mining or to increase the acceptance of the lignite industry in general.