Beitrag zur Analyse des Eigenspannungsverhaltens von Composite-Hochdruckspeichern mit metallischem Liner
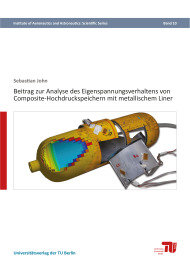
Size: 183 pages
Format: 17,0 x 24,0 cm
Publishing year: 2020
ISBN 978-3-7983-3179-2Format: 17,0 x 24,0 cm
Publishing year: 2020
19,00 €
When designing high-pressure vessels, the use of fibre reinforced plastics becomes of increasing importance due to their high specific strength properties. However, a high variation in material properties and manufacturing parameters as well as variable load scenarios during service life; make it very difficult to give accurate lifetime predictions and to define reasonable inspection periods. The aim of this work is to get detailed information on the residual stress behaviour in the context of the presented light-weight structure aging process. The research of this work focuses on pressure vessels which consist of an inner aluminium liner surrounded by carbon fibre reinforced plastics (type III). The lifetime of the structure is limited by the load cycle sensitivity of the metal and its residual stress condition. To be able to give more accurate lifetime predictions in the future, a lifetime analysis of residual stresses is executed to deliver input data for an appropriate structural durability model.
The central point of this research is an artificial aging testing program of type III pressure vessels, during which changes in residual stress conditions are measured and analysed continuously. In the beginning, mechanical peak loads as well as load-structure behaviour are obtained through preliminary tests and simulations. Next, for residual stress measurements, the underlying parameters had to be determined and tested. A focus is set on the development of a non-destructive measurement method based on an experimental modal analysis. Through experimental studies, the intensity and scatter of the initial residual stress condition of manufactured pressure vessels was obtained first. Then a significantly reduced residual stress condition was obtained when measuring 15-year-old specimen. Accompanying the artificial aging program, changes of residual stresses, altered material characteristics and strain behaviour of the tested structures were monitored. According to measurement results, an increased state of residual stresses due to artificial aging was determined. In a last step, the captured residual stress behaviour was implemented into a developed structural durability model. The used analytical model was verified by the number of load cycles until failure which have been obtained experimentally. By simulating cases of various load conditions, it is shown that the accuracy of lifetime prediction can be increased when considering variable states of residual stresses.